A Guide to Choosing the Right Cutting Edge for Your Plow
Created September 30, 2020
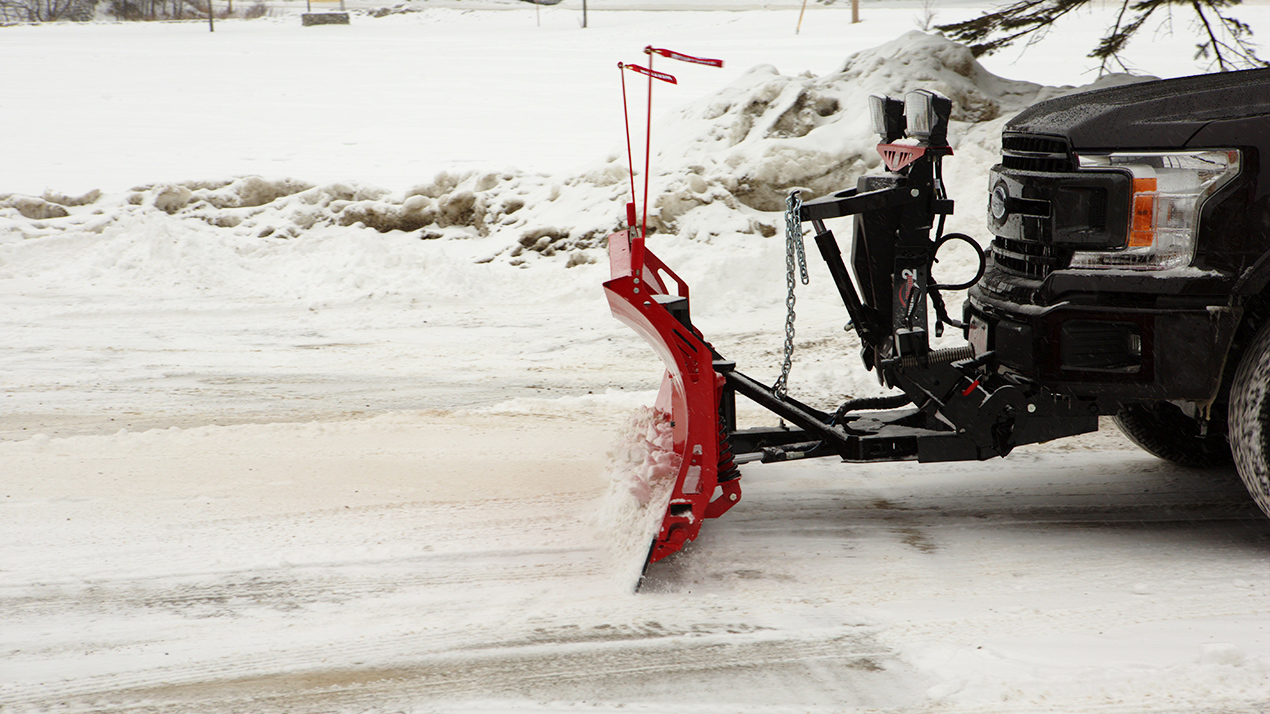
There are two main outputs contractors want out of their snowplow cutting edge—the longest life and the most efficient scrape. After reading this guide, you’ll understand which cutting edge is best for your setup and how to recoup your replacement costs accordingly.
Before you decide on the proper edge, you need to have the right plow for the job. Plows are designed for specific applications, so not all plows will provide the same cutting edge compatibility. For instance, a WESTERN® DEFENDER™ is ideal for homeowners and not intended for constant use like a PRO PLUS™ or WIDE-OUT™ that is meant for commercial properties. Ensuring you have the right setup for the application will help to increase productivity.
Replacement Cycle Factors
When figuring out cutting edge replacement frequencies, it’s not necessarily a matter of if you will need to replace it; it’s a matter of when. The material removal rate of a plow edge is dependent on the friction between the surface and the material in contact with the ground. The six variables that impact this rate are:
- Contact Pressure—The more pressure there is, the more wear on your cutting edge. Uneven surfaces increase contact pressure when a small portion of the blade is in contact with the surface. It may be ideal to go with a thicker edge or accessorize with a high wear shoe kit to increase surface area on the road. This spreads the weight of the plow across a greater surface to slow the cutting edge wear.
- Climate—Although there isn’t a lot you can control, you can be aware of how the climate impacts your cutting edge wear rate. A wet, slushy climate found in the coastal region will typically lead to surface conditions that reduce friction and wear. Where-as a high altitude climate that is cold and dry tends to produce plowing conditions that increase friction and increases wear.
- Surface Conditions—Friction is decreased and causes less wear on loose or wet surfaces. Solid, dry surfaces increase friction and cutting edge wear.
- Surface Material—Granite or hard, scratchy surfaces (like many municipal roads) wear cutting edges quicker than smoother or softer surfaces like asphalt or parking garage pavement.
- Speed—The faster you are traveling, the more heat is generated through friction which can increase the wear rate. When plowing a large, open warehouse parking lot with minimal obstacles, you can move faster versus a driveway where you need to slow down to accommodate the short distance increased obstacles.
- Cutting Edge Material—Each material type wears at a different rate. Some cutting edges are made from harder material and can withstand more than softer materials. For instance, you will replace rubber edges much more quickly than you would a carbide edge.
If you’re replacing your edge more than twice a season, you may want to look into other material options for your intended use. The more often you have to replace your cutting edge, the more down time for your business and the higher your cost of owning and maintaining your plow will be.




Signs You Need a New Cutting Edge
Before any event, complete a walk around inspection and check for cracks or damage to the edge. Monitor wear and replace the cutting edge before you get to the base angle that protects the blade of your plow, as uneven wear can negatively impact performance. Curb guards can help reduce uneven wear patterns and lengthen the life of your cutting edge.
Steel Cutting Edges
High carbon steel cutting edges, 1080 grade tensile strength as example, are the most common material type and come standard on all WESTERN plows. They are multi-purpose and resistant to bending and twisting, giving a clean scrape while minimizing damage to the property surface. These traditional edges are easily sourced and readily available so the replacement cost is relatively low, however you will need to replace them more frequently than harder materials such as specialty steels like AR400 or carbide.
Carbide Cutting Edges
This is the most durable cutting edge material. Made with tungsten for high-performance wear resistance, this cutting edge is meant for abrasive surfaces. Not every plow and application requires this tough of an edge, so it is only available for select plow models. Due to the strength of the cutting edge material, it can cause surface damage so it’s typically used on roads or surfaces that are repaved often. Since the material is less commonly available, it comes with a higher price tag. The higher initial price is balanced by longer life and can be well worth it if your steel edge is wearing out too quickly.
Rubber Cutting Edges
A rubber cutting edge is the most forgiving and delicate material, but can also wear quickly requiring frequent replacements. Due to the elastic tendencies of rubber, it glides over the surface rather than scraping into it. This can also result in residual snow remaining and may require additional salt application for a clean surface. With a higher replacement cycle, you’ll want to limit use to specialty properties where a rubber edge is required (like a parking garage).
Some builder guidelines and winter service contracts will specify how the pavement surface must be maintained. Improper maintenance could result in a potential safety issue. Since it’s not ideal to swap edges throughout the season, snow and ice contractors that accept this specialized work have dedicated equipment for these accounts and rubber edges are often part of the solution.
Poly Cutting Edges
Poly is a good middle-of-the-road cutting edge; it’s not as hard as steel but not as soft as rubber. This allows for a more effective scrape that is durable for longer distances than rubber. The main benefit to using a poly cutting edge is that it’s ideal for delicate or decorative surfaces. This type of surface is common in shopping malls, banks and sometimes even residential properties. Poly edges don’t last as long as steel but reducing the risk of damage is often worth the additional replacement and expense. Poly can vary greatly in terms of chemical makeup and quality. As a result, the price can also vary greatly.
Estimating Replacement Costs for Maximum Profitability
Before you can consider profitability, you need to establish good quality service—are you delivering the level of service you’re billing for? If the edge lasts longer but creates property damage or if you’re using an inexpensive cutting edge but replacing it multiple times throughout the season, you need to step back and think, what is the long term cost to your business? It’s probably not ideal to continue use with these situations due to the associated costs, labor and repairs needed by not having the proper edge.
In order to remain profitable and keep high quality service, you’ll need to build the replacement cost into your property estimates. Monitor wear for each cutting edge type to determine useable life and charge accordingly. You can do this by measuring the height of the cutting edge prior to the season. Measure the useable material in a few different areas across the length of the blade in case there is an uneven wear pattern from prior use.
After one month, go back and measure the useable material left and extend that to the rest of your season. As example, if you’re removing ½” of material per month in a four month season, you may not need to make any change. But, if your usage is causing wear of 2” or more per month, you may need to think about using thicker or harder material. You have to consider all factors when finding the perfect edge for your setup.
Beware of the “Too Good To Be True” Aftermarket Trap
As you may have noticed, not all cutting edges are created equal. When purchasing OEM cutting edges, you can rest assured knowing that they are designed for your specific plow and intended use. Although will fit parts may be inexpensive initially, it often comes down to quality and design. Lean on our expertise and trust WESTERN for all your OEM cutting edge and accessory needs.