3 Preventative Measures to Reduce Material Bridging & Spreader Damage
Created December 15, 2020
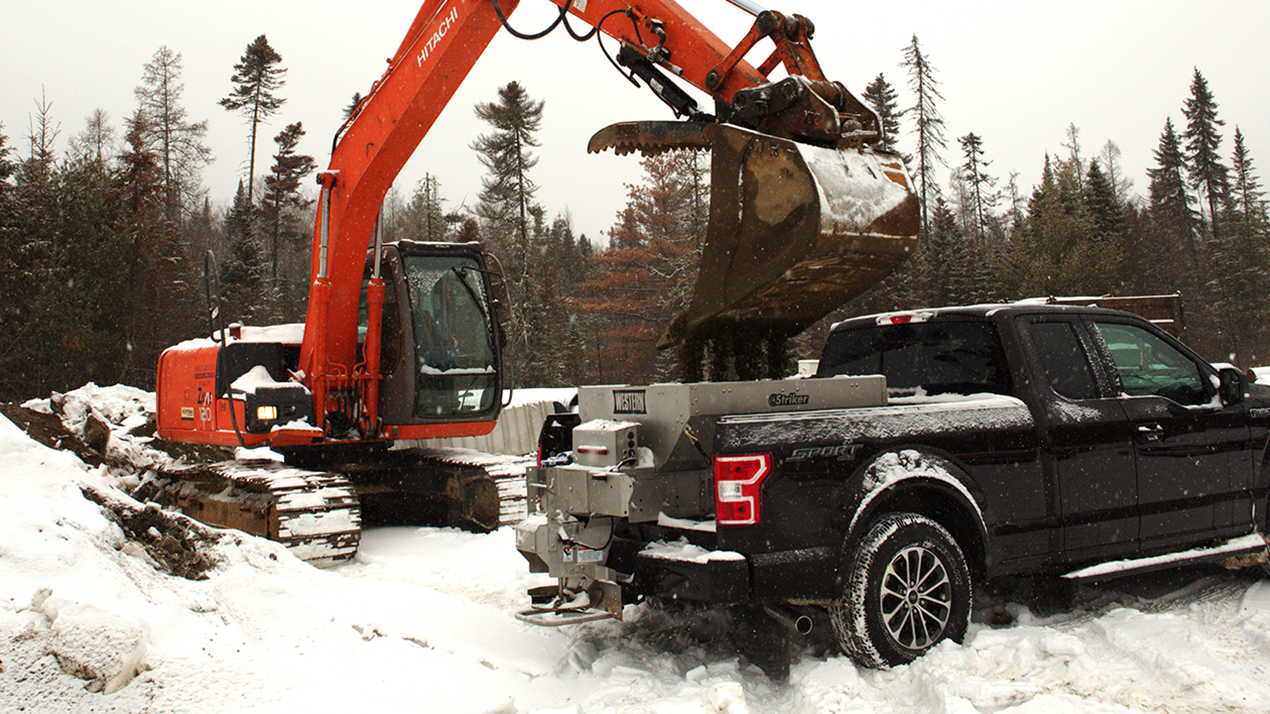
When snow is in the forecast, your operation is relied on to keep businesses and homeowner associations clear and accessible. In these situations, time is of the essence. Salting or sanding is likely a huge part of the winter services you provide to your customers—both before and during the storm. You don’t have time to deal with your salt, sand, or other material bridging and clogging in your spreader—messing with your ability to delivery anti-icing services.
#1: Wet De-Icing Material Can Cause Clogging
When you’re using salt and sand (or a combination) in freezing temperatures to combat snow and ice, any moisture contained within the de-icing material can freeze inside the hopper. When this happens, the material is unable to flow freely through the material delivery system. Estimating how much material you’ll need for the season and properly storing it is all about planning ahead.
To avoid moisture, store your de-icing material in stockpiles on waterproof pads so moisture doesn’t seep into the pile from the ground. The stockpile should be inside or covered by a waterproof material, such as a tarp. High humidity in the summer months should also be watched. When humidity is above 75%, salt and sand can absorb the moisture from the air.
To protect your salt (or sand) pile from runoff or melting snow, use sand bags or a trench around the pad your pile is resting on. Choosing a location for your pile that is over 50 feet away from major waterways will also protect the local environment and limit potential contamination. Check with your local government before constructing a large salt storage facility and be prepared to meet facility requirements or the DNR can fine you.
When looking for a new salt spreader, look for features that limit the elements from getting into the hopper and ensure the de-icing material is funneled directly towards the material delivery system. These features can include a weather-resistant cover, corrosion-resistant hopper, and an optimized material delivery system.
#2: Settling Material Becomes Hard-Packed & Difficult to Spread
When you fill your spreader with material, make sure you are ready to apply salt or sand. If you allow the material to stay in the hopper too long, the material’s own weight can pack it down making it difficult to spread. It might seem like filling the hopper as full as possible is the most efficient way to maximize salting jobs—but the added weight can pack down the de-icing material and increase the risk of bridging. If your material freezes and bridges, it will cost you time in the long run.
The design of the hopper, as well as the hopper material, can assist the salt, sand, or combination from settling. For larger capacity spreaders, the industry has been favoring hoppers made out of polyethylene (poly) because the material is naturally smooth and slippery. This aids the flow of salt/sand to the material delivery system for application.
Stainless steel hoppers are also readily available and do an excellent job applying salt and sand. They use the shape of the hopper and vibrators to ensure the material moves easily down to the material delivery system.
#3: Ensure Your Material is Coarse Enough
If your de-icing material is too fine, it will harden faster and clog up your spreader. Ensure that you are using the correct de-icing material for your spreader equipment. This includes coarse rock salt and coarse sand meant for creating traction.
One way to ensure your ice control equipment performs correctly when a winter storm is bearing down on you, is to ensure your de-icing material is stored and handled properly. This will greatly reduce the chance of salt and sand bridging that slow you down. If you want to ensure you have the correct spreader type for the material you apply, check out the WESTERN® spreader selector tool.